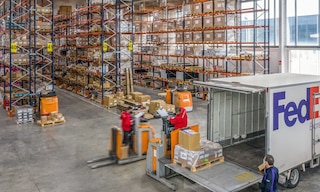
Zéro stock : comment réduire les stocks pour une meilleure efficacité
Le zéro stock est une stratégie logistique et de production qui vise à minimiser la quantité de stock dans l’entrepôt afin de réduire les coûts d’exploitation. L’objectif est de n’avoir aucun produit immobilisé qui ne soit déjà réservé à une commande.
Dans cet article, nous définissons ce qu’est le zéro stock, quels sont ses principaux avantages, comment l’appliquer à l’entrepôt et comment il est associé aux systèmes de production tels que le just-in-time (JIT) ou aux modèles e-commerce comme le dropshipping.
Définition du zéro stock ?
Le zéro stock, également appelé inventaire à stock zéro, est une stratégie de planification logistique qui vise à limiter autant que possible la quantité de stock détenue dans un entrepôt afin d’économiser de l’espace et d’éviter des coûts non productifs. Seuls les produits déjà commandés par les clients sont réceptionnés dans les installations logistiques, ce qui minimise le stock de réserve.
Le zéro stock est l’un des principaux objectifs des stratégies logistiques et des systèmes de production visant à supprimer des surcoûts, comme c’est le cas avec le just-in-time ou le cross-docking. Appliquées à des secteurs très concurrentiels tels que le e-commerce ou l’industrie manufacturière, ces stratégies ont pour but de maximiser les performances de tous les processus et d’éliminer les erreurs ou les dysfonctionnements qui augmentent les coûts d’exploitation.
Le modèle just-in-time, développé à l’origine par Toyota, a été le pionnier dans la mise en œuvre des stratégies de zéro stock dans le cadre d’un système organisationnel visant à atteindre une productivité maximale par l’élimination des dépenses superflues. Cette philosophie de production s’est illustrée dans ce que l’on appelle la théorie des cinq zéros : zéro défaut, zéro panne, zéro délai, zéro papier et zéro stock.
Avantages (et inconvénients) de la politique du zéro stock
La stratégie du zéro stock favorise la réduction des stocks dans l’entrepôt, pour permettre :
- D’éviter les pertes de stock dues à la détérioration de la qualité ou à la baisse de la demande, ce qui est particulièrement vrai pour les entreprises qui travaillent avec des denrées périssables ou avec des délais d’expédition courts, comme dans les secteurs de l’agroalimentaire ou de l’automobile, ou dans des secteurs où les promotions et les fluctuations de la demande sont fréquentes, comme la mode et le retail.
- De réduire les coûts de stockage, car le besoin de garder des stocks de marchandises est considérablement diminué. La stratégie du zéro stock implique moins d’emplacements et donc une plus petite surface de stockage. L’espace excédentaire peut être utilisé pour d’autres opérations qui contribuent au développement de l’activité, comme l’agrandissement de la zone de production ou des zones de réception et d’expédition. Il est également possible d’aménager une zone de transit comme zone tampon, c’est-à-dire une zone de stockage provisoire où les marchandises sont déposées en attendant la prochaine opération.
- D’optimiser le capital humain : la mise en œuvre de cette politique de gestion des stocks permet de réaffecter les opérateurs sur des tâches à plus grande valeur ajoutée.
Cependant, la stratégie du zéro stock exige une précision pointue dans la logistique d’approvisionnement. Tout écart entre les ordres d’entrée et de sortie entraîne une rupture de stock et, par conséquent, l’impossibilité de livrer la commande au client. Effectivement, avec l’absence de stock de sécurité, les entreprises qui appliquent une politique de zéro stock ne disposent pas d’une logistique élastique et ne peuvent donc pas s’adapter aux pics inattendus de la demande.
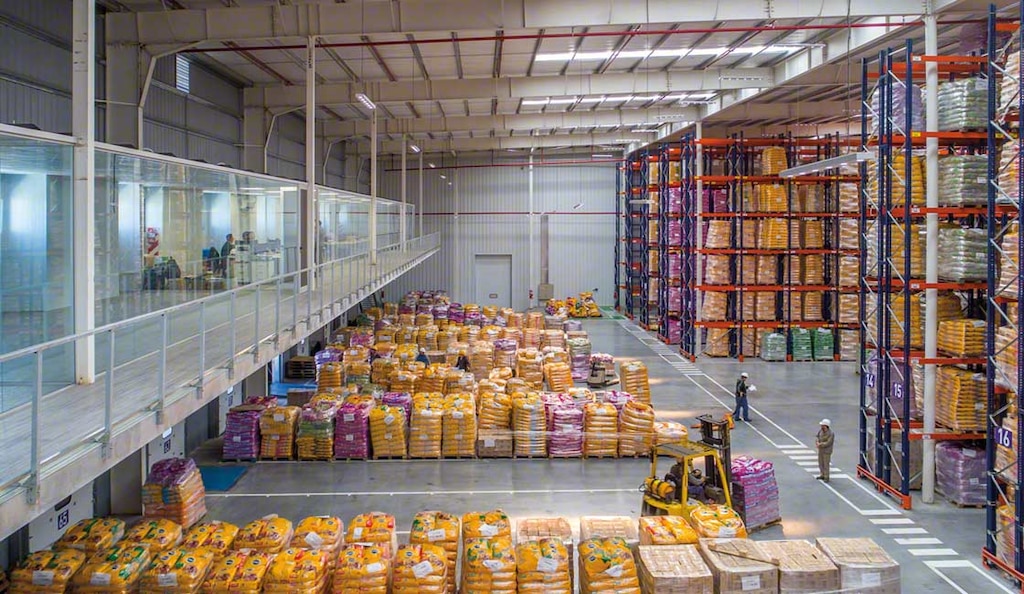
Du « just-in-time » au « cross-docking », 3 stratégies pour mettre en application le zéro stock
Le principe de diminution des stocks de l’entrepôt pour baisser les surcoûts est l’un des éléments clé de nombreuses politiques de gestion des stocks qui abondent dans le scénario logistique actuel. Voici les principales :
- Just-in-time : une méthode d’organisation de la production selon laquelle il ne faut disposer que du stock ou du produit fini nécessaire au traitement des commandes. Dans la stratégie JIT, les marchandises arrivent en quantité nécessaire et au bon moment pour exécuter les opérations de production.
- Cross-docking : une méthode de préparation des commandes qui permet d’expédier les marchandises, directement chez le client sans passer par une phase de stockage préalable, de cette manière le stock reste le moins longtemps possible dans l’entrepôt. L’entrepôt reçoit les marchandises, les place dans une zone tampon (ou zone de transit) et les expédie directement sans les stocker dans les rayonnages. Ce système d’organisation nécessite une synchronisation parfaite de tous les maillons de la chaîne logistique et c’est là que digitaliser sa logistique devient un élément essentiel pour éviter les erreurs et les ruptures de stock.
- Dropshipping : un mode de vente en ligne qui permet de commercialiser des produits sans les avoir en stock. Dans ce modèle économique, le vendeur (dropshipper) gère uniquement la transaction, agissant comme un intermédiaire entre le client qui achète le produit et le fournisseur qui détient les produits. C’est le fournisseur qui est chargé d’expédier la commande à l’acheteur, au bon moment, et dans les conditions convenues. Par conséquent, le dropshipper ne gère ni ne stocke les biens qu’il commercialise : son stock est nul.
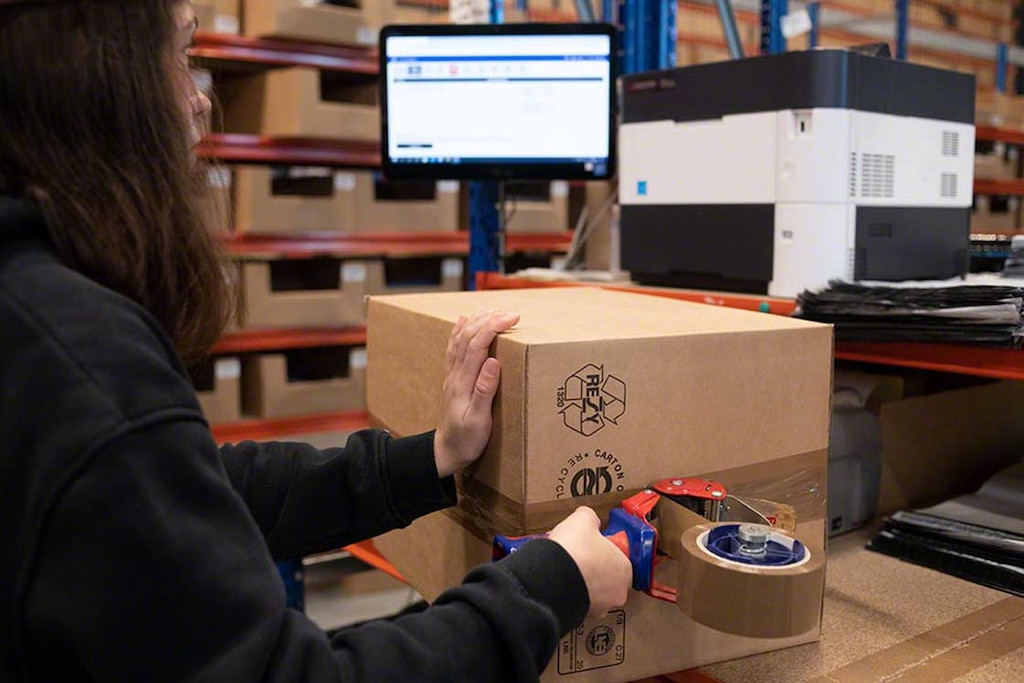
Comment mettre en place une stratégie de zéro stock ?
Dans une stratégie de zéro stock, assurer une gestion efficace des stocks est essentielle, ce qui nécessite de remplacer le contrôle manuel des stocks par des systèmes numériques capables de coordonner les ordres d’approvisionnement avec les commandes. Toutes les opérations de l’entrepôt ou du centre de production doivent aller de pair pour minimiser les niveaux de stock et assurer l’approvisionnement. Un logiciel de gestion d’entrepôt (WMS) est l’outil idéal pour contrôler avec précision la réception et l’expédition des produits, la gestion des emplacements de stockage et la préparation des commandes.
Un autre pilier de la stratégie zéro stock consiste à réduire le lead-time, c’est-à-dire le délai moyen d’approvisionnement en produits et/ou en matières premières. Pour y parvenir, il est également fondamental de disposer d’un WMS en contact permanent avec le logiciel du fournisseur, ce qui réduit les délais d’approvisionnement et permet de coordonner le réapprovisionnement en fonction des commandes.
En somme, la mise en place d’un logiciel de gestion d’entrepôt est la meilleure façon d’atteindre le zéro stock. Le logiciel permet la traçabilité de toutes les opérations de l’entrepôt et il permet en particulier, au responsable logistique d’avoir une visibilité globale des niveaux de stocks requis pour l’expédition ou pour la production, et de connaître les stocks réels de l’entrepôt.
Exemple d’inventaire zéro : Font Vella
Leader des eaux minérales en Espagne, Font Vella a confié à Mecalux la réorganisation de la logistique de son entrepôt de Sant Hilari Sacalm (Gérone). Le site a une capacité de plus de 4 200 palettes d’eau en bouteille et 500 palettes d’eau en bouteille de verre, soit environ l’équivalent d’une journée de production. Cela contraint l’entrepôt de stockage de distribuer les marchandises en continu afin d’empêcher la formation de goulots d’étranglement en production.
En pratique, cette usine utilise la méthode de préparation de commandes cross-docking : le produit arrive déjà palettisé à l’entrepôt, qui l’expédie tel quel le jour même. En fait, comme la production ne s’arrête pas, même le week-end, les opérateurs veillent à ce que l’entrepôt soit complètement vide le vendredi, car les produits finis du samedi et du dimanche doivent être stockés dans l’entrepôt.
La solution fournit par Mecalux est des rayonnages à palettes dynamiques qui font office de zone tampon. Les palettes produites pendant la journée sont stockées dans les rayonnages, en attendant d’être expédiées en fin de journée.
Zéro stock : moins de coûts, mais plus de risques
La stratégie logistique et de production zéro stock présente de nombreux avantages pour les entreprises sachant la mettre en œuvre. Elle permet notamment, l’optimisation des ressources ou la diminution des coûts de stockage. Cependant, si elle n’est pas correctement exécutée, elle peut entraîner des écarts de stocks et des erreurs dans la préparation des commandes pouvant nuire à la compétitivité et à l’image de l’entreprise.
C’est pourquoi, il est essentiel de remplacer les procédures de gestion manuelles par un logiciel de gestion d’entrepôt capable d’assurer un contrôle strict du stock de l’entrepôt. Ce logiciel coordonne toutes les tâches de l’entrepôt, en assurant le réapprovisionnement des produits pour chaque emplacement, en synchronisant les ordres d’approvisionnement avec les ordres de production ou d’expédition pour une productivité maximale de l’installation.
Si vous êtes intéressé par la mise en place d’une politique d’inventaire zéro, n’hésitez pas à contacter Mecalux. Nos experts vous guideront dans le choix de la meilleure solution pour votre entreprise.