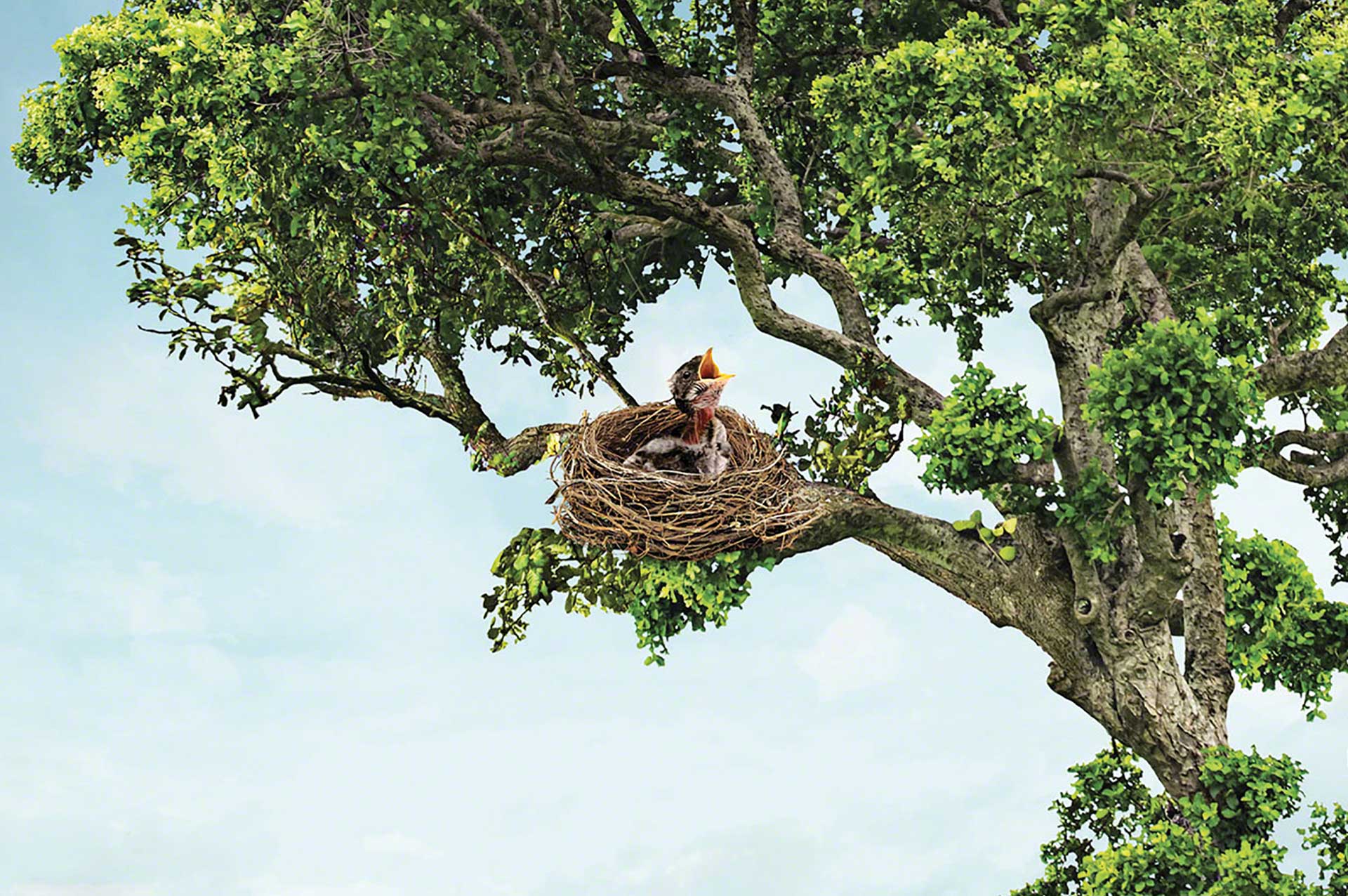
Konya Şeker construit un entrepôt automatique parasismique
Konya Şeker, plus grand fabricant de sucre turque, connecte son usine de production à son entrepôt automatique parasismique de 38 m.
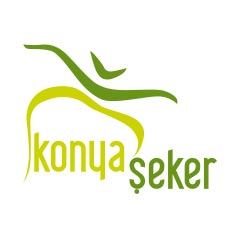
Konya Şeker, plus gros fabricant de sucre en Turquie, a modernisé la logistique de son centre de Çumra avec un entrepôt automatique parasismique de 38 m. Connecté aux lignes de production, l'entrepôt accélère la distribution quotidienne de 2 000 palettes de confiseries et biscuits.
Konya Şeker : leader turc de la production sucrière
Konya Şeker est une entreprise turque qui produit et commercialise du sucre et ses dérivés. Elle fabrique également une large gamme de confiseries, incluant des chocolats, des biscuits et des halvas (pâtisseries orientales à base de sésame), en utilisant son propre sucre. Depuis 2008, Konya Şeker appartient au groupe Anadolu Birlik Holding (ABH), qui opère dans des secteurs aussi variés que l’agroalimentaire, l’agriculture, l’énergie et la chimie. Fondée en 1954, Konya Şeker a 45 installations, 900 000 agriculteurs et plus de 10 000 salariés.
DÉFIS
|
SOLUTIONS
|
AVANTAGES
|
---|
Au cours des dernières décennies, Konya Şeker a profondément transformé ses opérations de logistique et de production en s’appuyant sur les dernières technologies les plus récentes et une forte volonté d’automatiser ses processus robotiques. Cette modernisation de la chaîne d’approvisionnement a facilité à l’entreprise d’augmenter sa production et de devenir le leader turc de la production de sucre, tout en lui permettant de mener à bien un ambitieux plan d’expansion. Konya Şeker compte aujourd'hui 45 sites de production qui génèrent environ 22 % du sucre consommé en Turquie. L'entreprise est également leader sur le marché des pommes de terre surgelées.
Située dans la petite ville de Çumra, à proximité de Konya, l'usine de Konya Şeker est la plus grande usine de sucre de Turquie. Elle s’étend sur 260 hectares et compte 27 lignes de production. « Au cours des dernières années, nous avons doublé notre production annuelle de sucre pour atteindre 435 500 tonnes. Toutes les machines et tous les équipements proviennent des meilleurs fournisseurs de technologies de pointe d’Europe. C'est également la seule usine de sucre au monde capable de s'approvisionner en matières premières dans un rayon de 20 km », explique Kerim Başaran, responsable de l’entrepôt automatisé de Konya Şeker.
L’usine de Çumra abrite aussi le centre de production de la marque de chocolats et de biscuits de Konya Şeker. « Nos installations de production de chocolat Torku, équipées des technologies les plus modernes, approvisionnent le marché local et nous permettent d’exporter nos produits vers 74 pays, dont la Suisse, une référence mondiale en matière de chocolat », affirme M. Başaran à l’adresse.
Ces dernières années, Konya Şeker a élargi et diversifié sa gamme de produits Torku en y ajoutant des bonbons, des produits laitiers, de la charcuterie, des viennoiseries, de l’huile et du vinaigre, entre autres. Cette diversification o entrainé une augmentation de la production et a conduit l’entreprise à accorder la priorité à la logistique. Au départ, elle gérait les matières premières et les produits finis dans un entrepôt traditionnel. Cependant, face à la nécessité de réduire les délais d’entrée et de sortie des marchandises, l’entreprise a décidé d’investir dans des technologies intralogistiques.
Dans le cadre de sa stratégie de modernisation, Konya Şeker a construit un entrepôt automatisé autoportant géré par le logiciel Easy WMS de Mecalux, avec lequel elle distribue 2 000 palettes par jour. Capable de stocker 48 000 palettes de biscuits et de chocolats, l’entrepôt est directement intégré au centre de production, ce qui facilite l’échange automatisé de matières premières et de produits finis prêts à être distribués.
Outre l’augmentation des performances, la technologie a contribué à maximiser la qualité des confiseries en garantissant le respect de protocoles de sécurité et d’hygiène rigoureux. « Nos priorités sont de produire un chocolat naturel sans additifs, en préservant ses propriétés. Pour y parvenir, il est essentiel de veiller au respect de la législation en vigueur », indique M. Başaran.
Un entrepôt automatique antisismique
La majeure partie du territoire turc se situe sur la plaque tectonique d’Anatolie, coincée entre les plaques eurasiatique, arabe et africaine. Les frottements entre ces plaques font de la Turquie l’une des régions les plus exposées aux tremblements de terre au monde.
L’entrepôt de Konya Şeker est autoportant, c’est-à-dire que les rayonnages supportent leur propre poids, ainsi que celui des murs et, ainsi que les marchandises. Dans sa conception, certains facteurs qui interagissent sur sa structure ont été pris en compte, comme la force du vent et, dans ce cas précis, le degré sismique correspondant à la zone de l’installation et aux réglementations locales en vigueur.
Eriger un entrepôt de 38 m de haut dans une région à forte sismicité comme Konya a constitué un défi majeur pour le département d’ingénierie structurelle de Mecalux. La construction a nécessité une grande précision. Les rayonnages ont été renforcés et des montants centraux plus robustes ont été installés pour absorber les forces dynamiques générées par d’éventuels mouvements sismiques.
Maximiser les performances de stockage de Konya Şeker
« Grâce à l’automatisation, nous avons réduit nos délais de stockage et de récupération », manifeste M. Başaran. L’entrepôt automatisé de Konya Şeker se compose de sept allées de 138 m de long équipées des rayonnages à double profondeur. Des transstockeurs Mecalux dotés de fourches télescopiques circulent dans chaque allée pour stocker et déstocker les palettes, accédant ainsi à la deuxième position de tous les niveaux. Pilotés par Easy WMS, ces machines atteignent des vitesses de déplacement de 220 m/min et d'élévation de 64 m/min.
Deux des allées sont dédiées aux matières premières et aux emballages, tandis que les cinq autres allées stockent les produits finis. Trois d’entre elles sont maintenus à une température contrôlée de 15 °C pour préserver la consistance, le goût et l’odeur des chocolats, tandis que deux autres allées fonctionnent à température ambiante.
Le logiciel Easy WMS gère les emplacements de stockage des produits en fonction de leurs dimensions et leurs rotations A, B et C. Les produits à forte rotation sont stockés à proximité des points d'entrée et de sortie, tandis que ceux à faible rotation sont placés à l'extrémité opposée des allées, optimisant ainsi les déplacements des transstockeurs.
Connexion automatique à la production
L’un des principaux atouts de l’automatisation de l’entrepôt de Konya Şeker réside dans son intégration avec le centre de production, lui-même divisé en deux zones distinctes : une réservée aux chocolats et l’autre aux biscuits.
Pour assurer un flux ininterrompu de mouvements, un tunnel surélevé à 6 m de hauteur relie les sorties de la production de chocolat et de biscuits à l’entrepôt. À l’intérieur, un circuit de convoyeurs automatiques longe l’installation logistique. Grâce à leur capacité d’accumulation, les palettes peuvent y rester temporairement, en attendant d’entrer dans l’entrepôt, de manière ordonnée et sans qu’il soit nécessaire de les déposer au sol. Des élévateurs, situés au début et à la fin du tunnel, assurent le transfert les marchandises entre les différents niveaux.
L’usine de préparation de commandes automatisée de Konya Şeker
Konya Şeker est responsable de l’approvisionnement quotidien des supermarchés et magasins de Turquie en produits. Un bâtiment de deux étages est situé à l’une des extrémités de l’entrepôt. Le niveau supérieur est dédié à la préparation des commandes et le niveau inférieur aux expéditions.
L’étage dédié à la préparation de commandes comprend quatre blocs de canaux dynamiques pour les produits les plus populaires. Une navette automatique alimente chaque canal, qui peut stocker jusqu'à trois palettes d'une même référence, garantissant ainsi une réserve permanente de marchandises. Les opérateurs accèdent directement aux palettes par le bas des canaux et prélèvent les articles composant chaque commande. Assistés par des préparateurs de commandes, ils parcourent les allées et localisent les références indiquées par le logiciel de gestion d'entrepôt Easy WMS de Mecalux via des terminaux radiofréquence.
Devant les allées de stockage, des convoyeurs acheminent les références, les moins demandées, requises vers trois postes de préparation de commandes. Les opérateurs peuvent y préparer jusqu’à douze commandes simultanément.
Une fois finalisées, les palettes sont filmées puis stockées en attente d'affectation d'un itinéraire par Easy WMS. Elles sont ensuite dirigées vers la zone d'expédition située au niveau inférieur du bâtiment.
Le niveau inférieur du bâtiment annexe à l'entrepôt est consacré aux marchandises sortantes. Une navette les trie et les séquence dans 26 canaux dynamique de pré-chargement. Les palettes sont regroupées dans chaque canal, en fonction de leur appartenance à une même commande ou à un même itinéraire, prêtes à être chargées dans les camions.
Le logiciel de gestion d’entrepôt de Mecalux joue un rôle clé dans l’ensemble du processus logistique de Konya Şeker : « Avec Easy WMS, nous contrôlons plus rigoureusement les 48 000 palettes stockées dans l’entrepôt automatique, ce qui garantit l’exécution rapide et sans erreur de toutes les opérations », explique Başaran.
Pour améliorer la gestion des marchandises, le logiciel communique avec l’ERP de Konya Şeker. L’ERP informe Easy WMS à l’avance de l’arrivée d’articles de production dans l’entrepôt automatisé afin qu’il puisse leur attribuer des emplacements plus rapidement.
Konya Şeker met sa logistique au niveau d’une entreprise de premier plan
« Notre gamme Torku s'est imposée auprès des consommateurs grâce à ses produits 100 % naturels, sûrs et de haute qualité. Nous les fabriquons en contrôlant l'intégralité du processus, de la graine à la table, garantissant leur pureté et le travail des agriculteurs d'Anatolie », affirme M. Başaran.
L’entrepôt automatisé de 38 mètres de haut a marqué un tournant dans la chaîne d’approvisionnement de Konya Şeker et, en particulier, des chocolats et biscuits Torku. L’automatisation et la numérisation de la logistique sont des outils fondamentaux qui pour que l’entreprise atteigne ses objectifs. Grâce à ces technologies, elle assure un suivi exhaustif de ses produits et améliore l’efficacité de ses processus opérationnels avec un objectif clair : distribuer 2 000 palettes par jour dans 74 pays.
Avec Easy WMS, nous contrôlons plus rigoureusement les 48 000 palettes stockées dans l’entrepôt automatique, ce qui garantit l’exécution rapide et sans erreur de toutes les opérations.
Galerie
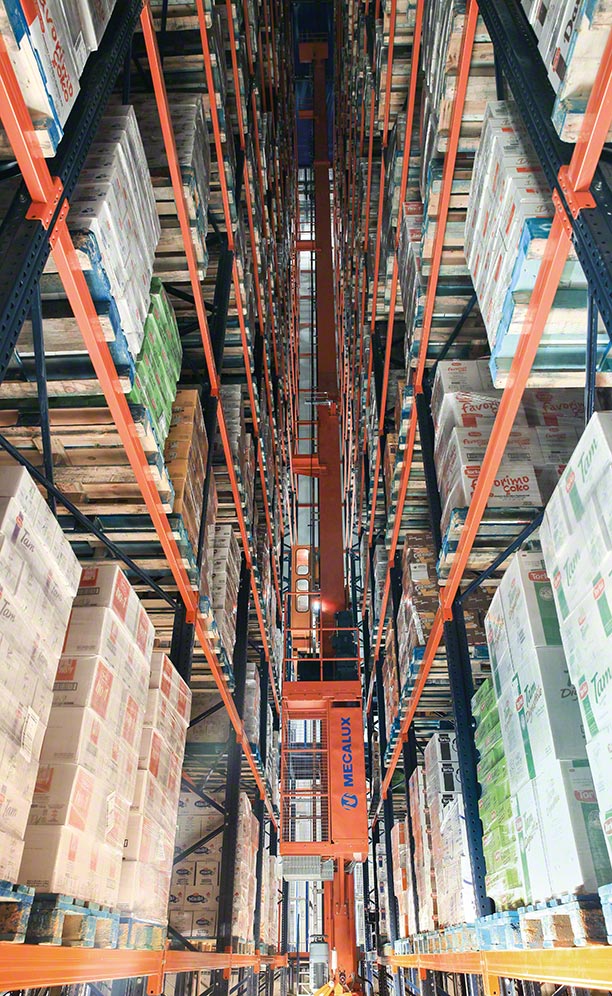
Le transtockeur déplace les palettes à l'intérieur des allées de stockage de Konya Şeker
Demandez conseil à un expert