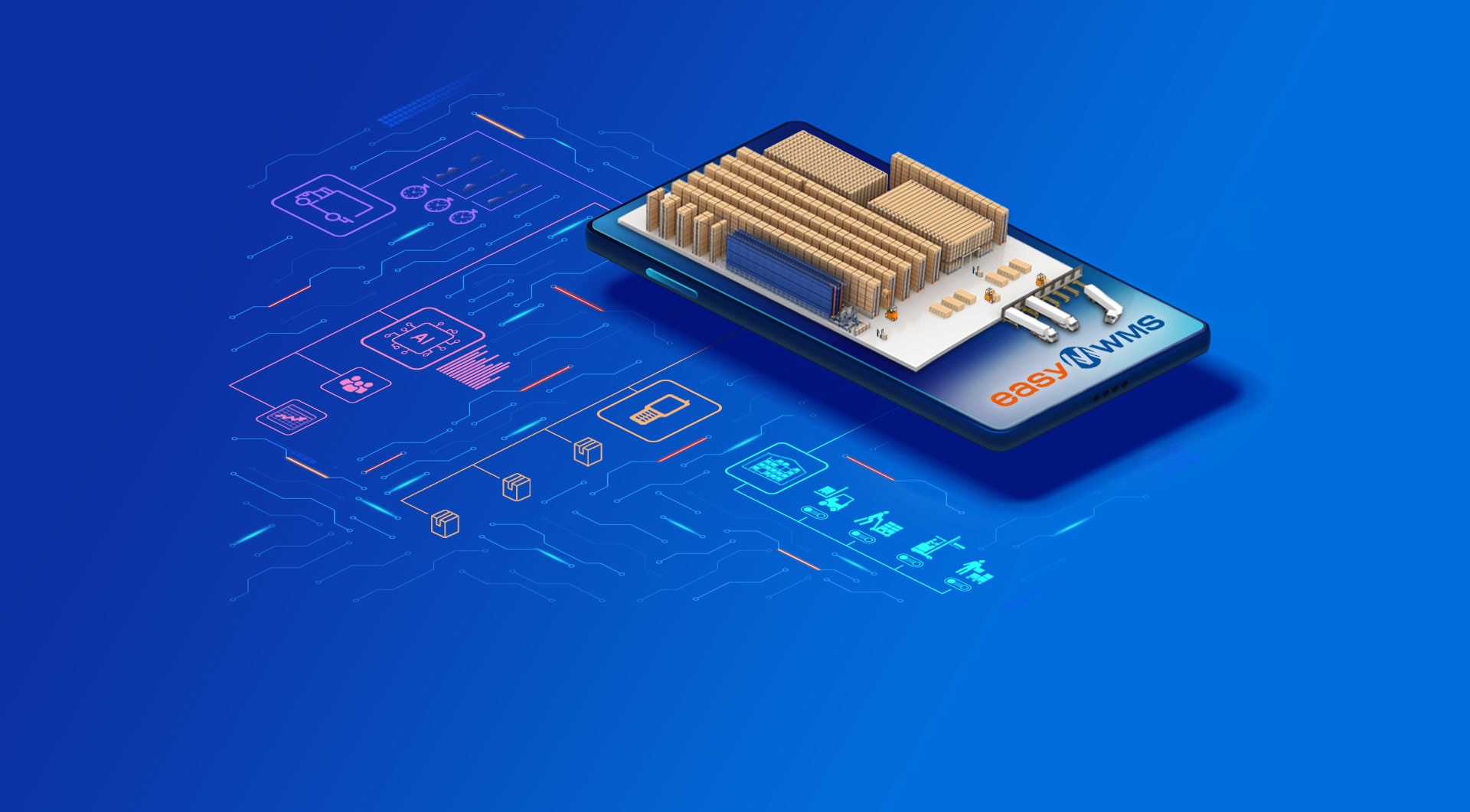
Cofan - un exemple de réussite pour les entreprises qui doivent gérer de grandes quantités de références
La nouvelle organisation logistique a permis à l'entreprise de réduire ses coûts d'exploitation et d'atteindre son objectif : proposer un service de livraison en 24 heures à ses clients.