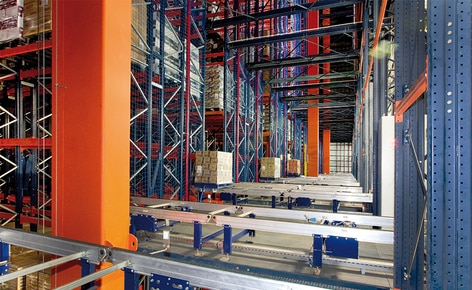
Le groupe agroalimentaire Grupo Siro a augmenté sa capacité et sa productivité grâce à un entrepôt autoportant de 35,5 m de hauteur
Grupo Siro poursuit sa croissance en s'équipant d'un entrepôt automatisé autoportant
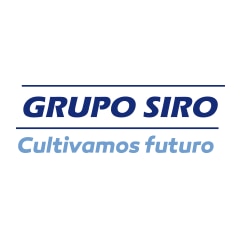
Mecalux a construit un entrepôt autoportant de grande hauteur entièrement automatisé pour Grupo Siro, l’une des plus grandes entreprises du secteur agroalimentaire en Espagne. Le nouveau bâtiment a été construit dans l’objectif de répondre à une croissance durable du Groupe, qui a décidé d’allouer ses investissements dans la création d’un entrepôt à la pointe de la technologie afin d’offrir un service de qualité à ses clients.
Présentation de Grupo Siro
Grupo Siro est l'un des fabricants de biscuits, de pâtes, de pain de mie, de viennoiseries et de céréales les plus importants d’Espagne.
C’est en 1991 que la société a fait l’acquisition de Galletas Siro qui appartenait au Groupe Danone. Elle a orienté sa stratégie sur l’innovation et l’utilisation des nouvelles technologies dans tous ses processus opérationnels, afin de proposer des produits au meilleur rapport qualité/prix à ses clients.
Actuellement, elle propose une gamme de références de 300 produits variés et compte 13 centres de production, un entrepôt logistique, un centre de R&D, un centre de valorisation de produits dérivés, deux espaces de bureaux et le siège de la Fondation Grupo Siro.
Besoins du client
Ces dernières années, l’entreprise a connu un essor important, dû principalement à une demande croissante de son client principal : la chaîne de supermarchés Mercadona.
Cette croissance et l’augmentation consécutive de la production ont saturé les espaces de stockage disponibles des entrepôts, généralement situés à l’intérieur des usines. Pour soutenir son rythme de production, l’entreprise avait d’abord pensé à externaliser l’entreposage chez un prestataire, mais cette solution n’offrait pas la flexibilité souhaitée dans le traitement de sa chaîne logistique et augmentait les coûts opérationnels.
Grupo Siro a sollicité Mecalux pour construire son nouveau centre logistique situé au sein de son siège à Venta de Baños (Espagne), afin d’améliorer la capacité de stockage de ses usines et d’augmenter l’efficacité et la performance de l’entreprise.
Solution proposée
Le département technique de Mecalux, en collaboration avec l’équipe logistique de Grupo Siro, a analysé dans les détails les besoins, les contraintes et les possibilités, et se sont orientés vers la solution suivante : la construction d’un entrepôt autoportant de 36 mètres de hauteur desservi par des transstockeurs et des convoyeurs pilotés par le logiciel de gestion d’entrepôt Easy WMS de Mecalux.
Le centre logistique est stratégiquement situé dans un cercle de 3 km de rayon dans lequel se trouvent quatre de ses principales usines, et à moins de 100 km de trois autres, ce qui facilite et accélère le transport du chargement entre les usines et le centre logistique.
Le flux de déplacements étant très intense et continu, deux quais de réception ont été aménagés sur une partie latérale de l’entrepôt, séparés des neuf quais d’expédition pour éviter les interférences entre les deux opérations, avec un vaste espace qui facilite les manœuvres de transport et l’attente des camions.
Le bâtiment annexé à l’entrepôt est formé de deux étages, ce qui favorise une organisation optimale des différentes opérations qui s’y déroulent :
- Le rez-de-chaussée est principalement destiné à la réception et à l'expédition de la marchandise et dispose d’une grande zone de préchargements au sol.
- C’est au premier étage que les palettes provenant des quais du niveau inférieur entrent dans l’entrepôt. Une zone a également été prévue pour le picking.
L’entrepôt
Les dimensions de l’entrepôt sont conséquentes : 102 mètres de longueur, 57 mètres de largeur et 35,5 mètres de hauteur, le maximum admis par la norme locale. Il est divisé en huit allées équipées des deux côtés de rayonnages double profondeur, chacun possédant 14 niveaux de charge de différentes hauteurs en fonction de la dimension des palettes de Grupo Siro : cinq niveaux pour des europalettes de 1 400 mm de hauteur, huit de 2 000 mm et un de 2 500 mm. Les unités de charge pèsent en moyenne 800 kg et au maximum 1 000 kg.
Chaque allée est équipée d’un transstockeur bicolonne avec fourches télescopiques et d'une cabine de maintenance embarquée dans la nacelle. Cet engin se charge de stocker chaque palette à l’emplacement qui lui a été assigné selon sa taille et sa rotation.
Deux circuits de convoyeurs complètent l’automatisation de l’entrepôt : l’un situé au rez-de-chaussée où sont déposées les palettes à expédier et l’autre à l’étage, à 6,7 mètres de hauteur, qui relie toutes les entrées en plus des sorties vers la zone de picking.
Les espaces libres entre les charpentes, situés dans la partie supérieure de l’entrepôt, permettent le passage des conduits de climatisation qui règlent la température de toute l’installation et redistribuent l’air correctement.
À l’extérieur, sur la partie arrière du bâtiment, ont été aménagés quatre équipements de pompage pour le système de lutte contre l’incendie, et un réservoir d’eau d’une grande capacité pour les dimensions de l’entrepôt. À l’intérieur se trouvent les gicleurs et les détecteurs qui évitent tout début d’incendie.
Le rez-de-chaussée
Distribution du rez-de-chaussée :
- Quai de déchargement automatique
- Quai de déchargement classique
- Quais de chargement (9 au tout)
- Zone de contrôle d’entrée des palettes et élévateur
- Sorties des palettes depuis l’entrepôt
- Zone de préchargement au sol
- Circuit virtuel de chariots LGV
- Accumulation des palettes vides
- Réception et conditionnement des palettes d’entrée
Entrée des marchandises
L’entrée des marchandises provenant des différents centres de production les plus proches est effectuée depuis les deux quais de réception, l’un à déchargement automatique des camions et l’autre manuel à l’aide de chariots élévateurs ou de transpalettes.
La zone de déchargement a une capacité d’accumulation de deux camions complets, soit un total de 66 palettes, qui sont dirigées vers la zone d’inspection pour validation de leur état.
Toutes les palettes passent obligatoirement par la zone d’inspection où sont vérifiés leur état, leur poids et leurs dimensions, qui doivent correspondre aux exigences de qualité de l’entrepôt. Si la palette est conforme, le système de contrôle donne l’ordre de la déplacer jusqu’à l’élévateur, qui la transporte à l’étage supérieur où elle entrera dans le magasin automatique.
Une palette rejetée au contrôle peut être dirigée vers trois zones différentes en fonction de l’anomalie détectée :
- La zone de reconditionnement.
- La zone d’accumulation où sont corrigés les surplombements qui dépassent les limites prévues.
- Le remontage de palettes : si la base des unités de charge n’est pas adéquate, les remonteurs la déposent sur une autre, en bon état. Ces palettes retournent à la zone d’inspection et sont à nouveau vérifiées avant d’accéder à l’étage supérieur.
La palette défectueuse et sans possibilité de correction est transportée jusqu’à la zone de sortie et expulsée du circuit.
Les palettes reconditionnées passent à nouveau par le poste d’inspection pour revérifier qu’elles respectent les exigences de l’entrepôt.
Il faut s’assurer que la marchandise qui entre dans le magasin automatique est la bonne et contrôler que le chargement ne déborde pas plus que prévu.
Sorties de l’entrepôt / expéditions
Les chariots élévateurs (LGV) manipulent les palettes qui sortent de l’entrepôt, les recueillent aux points de sortie de chaque allée de stockage et les transportent vers la zone d’attente assignée sur l’un des neuf quais de chargement, en suivant un circuit virtuel préalablement programmé.
Le chariot définit sa trajectoire en émettant un signal laser que renvoient les déflecteurs situés à des points proches de l’itinéraire. Le système de gestion peut indiquer avec précision sa position et donner l’ordre de rejoindre les postes de recharge lorsque le niveau des batteries arrive à une limite établie. La connexion étant totalement automatique, le processus ne nécessite aucune intervention humaine.
Les opérateurs n’ont plus qu’à à charger les camions à l’aide de transpalettes pour introduire la marchandise dans le véhicule assigné par le logiciel de gestion d’entrepôt en fonction de son numéro de commande, de l’itinéraire à suivre, de son client, etc.
Le personnel confirme chaque opération et exécute les ordres à travers un terminal radiofréquence.
L’étage supérieur
Entrée dans l’entrepôt
Après son passage par la zone d’inspection, la marchandise provenant des quais de réception accède au premier étage à travers l’élévateur.
À ce niveau, un convoyeur principal distribue les références entre les convoyeurs d’entrée dans les différentes allées de stockage. Le circuit est à sens unique et sert également au déplacement des palettes qui quittent les allées et se dirigent vers les zones de picking. Organisation de l’étage supérieur :
- Élévateur
- Circuit interne de l’entrepôt
- Convoyeurs d’entrée ou de sortie de chaque allée
- Navette de la zone de picking
- Postes de picking
- Zone d’emballage et de reconditionnement
- Convoyeur principal d’entrée dans l’entrepôt
Zone de picking
Deux postes de picking groupés ont été installés, dans lesquels chaque opérateur peut préparer deux commandes simultanément. La zone est conçue pour un futur agrandissement si les besoins de Grupo Siro le requièrent.
Les postes de picking sont situés au-dessus de convoyeurs. Des deux côtés de l’opérateur se trouvent les tables de levage hydrauliques ajustables à une position ergonomique pour manipuler la marchandise. La préparation de commandes est ainsi beaucoup plus facile.
Chaque poste de picking possède son circuit d’accumulation. Des empileurs et dépileurs de palettes ont également été mis en place pour approvisionner la zone, ainsi que des postes d’attente pour les palettes qui sont sorties de l’entrepôt et attendent une alvéole libre dans le circuit du poste assigné.
Une fois la commande terminée, la palette réintègre le circuit de convoyeurs qui, après son passage par la filmeuse, la transportera à nouveau dans l’entrepôt jusqu’à ce que le système de gestion ordonne son expédition.
Le logiciel
L’entrepôt est géré par le logiciel Easy WMS de Mecalux et communique en permanence avec le système de planification de ressources de Grupo Siro. Il permet de contrôler, de coordonner et d’enregistrer l’ensemble des processus logistiques et opérations qui se déroulent dans l’entrepôt.
En plus de son côté pratique et opérationnel, le logiciel est conçu pour les fonctions suivantes :
- Contrôle absolu de la gestion de l'entrepôt.
- Gestion de l’entrée et de la sortie de la marchandise depuis les quais de chargement et de déchargement.
- Pose stratégique des unités de charge dans l’entrepôt suivant un contrôle des allées et de leurs emplacements.
- Enregistrement et ajustement du stock en temps réel.
- Conception de l’ordre de sortie de la marchandise et de son chargement dans le camion, transmis par un terminal radiofréquence.
- Optimisation des tâches d’après l’itinéraire de picking.
- Communication directe avec le fournisseur logistique de Grupo Siro.
- Coordination de toutes les données de référence (articles, propriétaires, fournisseurs, clients, etc.).
Les avantages pour Grupo Siro
- Diminution des coûts opérationnels : l’élimination des entrepôts externes et la centralisation des opérations dans un même centre logistique se traduisent par une performance plus élevée et un retour rapide sur investissement.
- Capacité maximale : la grande hauteur de l’entrepôt et l’utilisation de transstockeurs ont permis à Grupo Siro de multiplier sa capacité de stockage, qui s’adapte à sa production croissante.
- Gestion totalement automatisée : Grupo Siro a optimisé la performance de toute sa chaîne logistique, en centralisant ses opérations de réception, de stockage, de picking et d'expédition dans un même espace, gérées et contrôlées par Easy WMS.
- Sécurité maximale : les entrepôts automatiques offrent la protection maximale aux opérateurs et à la marchandise, contribuant ainsi à l’objectif de l’entreprise d’encourager les processus efficaces qui garantissent à tout moment la sécurité des personnes.
Entrepôt autoportant automatique de Grupo Siro, Espagne | |
---|---|
Capacité totale: | 40 320 palettes |
Dimensions de la palette: | 800 x 1 200 x 1 400/2 000/2 500 mm |
Poids max./ palette: | 1 000 kg |
Nb. de rayonnages: | 16 rayonnages à palettes double profondeur |
Nb. d'allées: | 8 |
Nb. de transstockeurs: | 8 |
Nb. de niveaux de charge: | 14 |
Longueur de l’entrepôt: | 101 m |
Largeur de l’entrepôt: | 57 m |
Hauteur de l’entrepôt: | 33,5 m |
Galerie
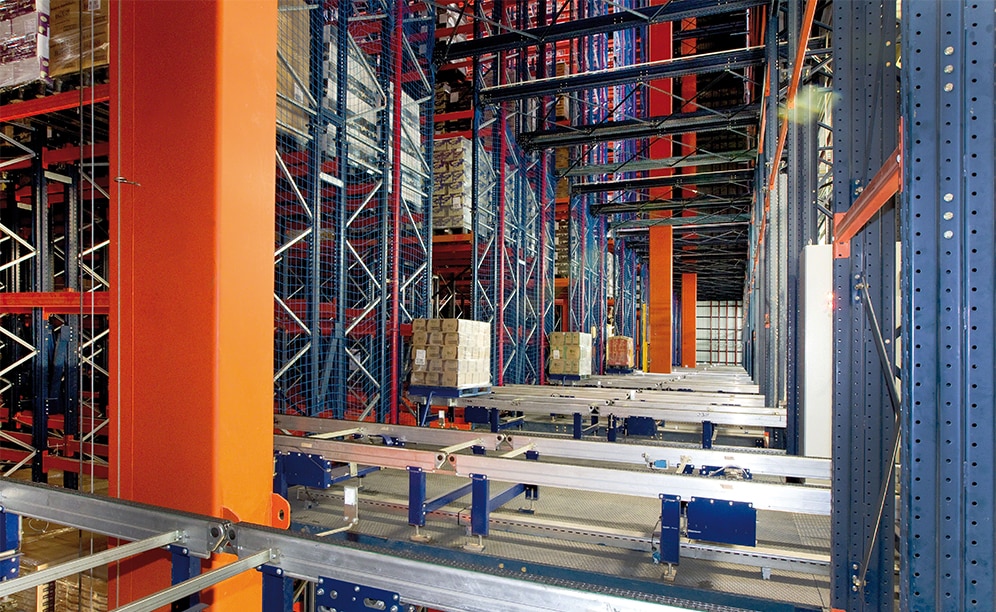
Mecalux a construit un entrepôt autoportant de grande hauteur entièrement automatisé pour Grupo Siro
Demandez conseil à un expert